Understanding the Importance of a Prototype Manufacturer
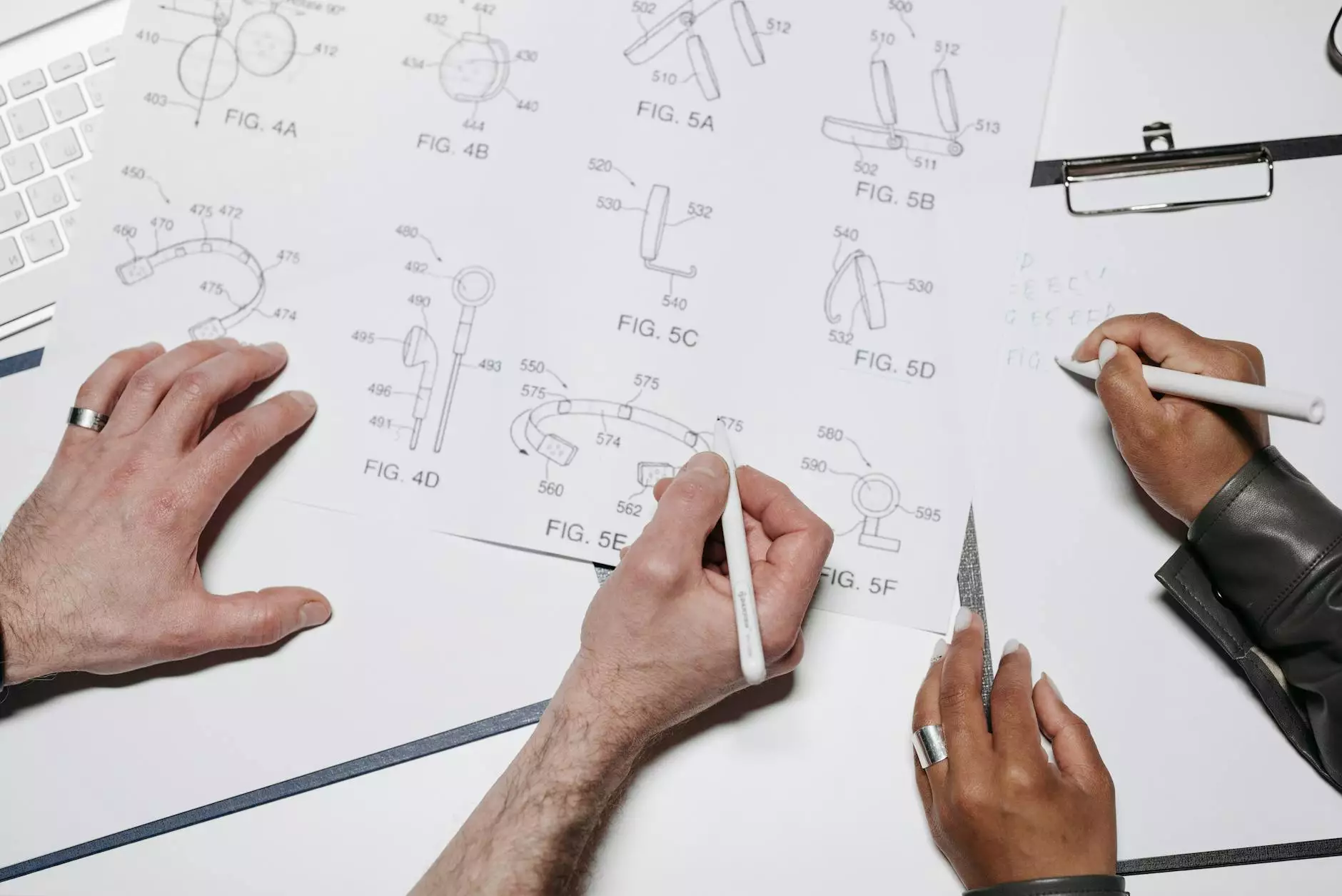
In today's competitive landscape, the role of a prototype manufacturer is more crucial than ever. Businesses across various sectors depend on effective prototyping to ensure their designs meet specifications and consumer expectations. This article delves into the multifaceted world of prototype manufacturing, offering insights into its processes, benefits, and best practices.
What is Prototype Manufacturing?
Prototype manufacturing refers to the creation of early models or samples of products before the mass production phase. This crucial step enables businesses to test concepts, evaluate designs, and identify potential issues early in the product development cycle. By engaging a specialized prototype manufacturer, companies can effectively streamline their design-to-production processes.
Key Benefits of Prototype Manufacturing
Choosing to work with a skilled prototype manufacturer offers numerous advantages:
- Identifying Design Flaws: Early prototyping allows for the discovery of design flaws that might lead to costly modifications later in production.
- Enhanced Communication: Producing a physical prototype enhances communication within teams and stakeholders, providing a tangible reference point.
- Market Testing: Prototypes can be presented to potential customers for feedback, ensuring the final product aligns more closely with market needs.
- Time and Cost Efficiency: By resolving issues early on, businesses can save time and reduce production costs significantly.
Different Types of Prototypes
Not all prototypes serve the same purpose. Understanding the types of prototypes available can help your business make informed decisions:
- Conceptual Prototypes: These are basic, often non-functional models used to visualize initial ideas.
- Visual Prototypes: Created to represent the physical appearance of a product, these prototypes focus on aesthetics rather than functionality.
- Functional Prototypes: These prototypes are fully operational and are used to test functionality and usability in real-world applications.
- Pre-production Prototypes: These are close-to-final versions that mimic the final product's production specifications.
Choosing the Right Prototype Manufacturer
Selecting a prototype manufacturer can significantly impact the success of your project. Here are some key factors to consider:
- Experience: Look for manufacturers with a proven track record in your industry.
- Technology and Equipment: Advanced technology can expedite the process and enhance the quality of prototypes.
- Material Options: The availability of various materials can affect the prototype's fidelity to the final product.
- Client Reviews: Testimonials from previous clients can provide insight into a manufacturer's reliability and quality of service.
The Prototype Manufacturing Process
Understanding the steps involved in prototype manufacturing enables businesses to appreciate the complexity and skill involved:
1. Design and Planning
The first step involves collaborating with engineers and designers to conceptualize the product. Drafting technical drawings and specifying materials are critical components of this phase.
2. Prototyping Technology Selection
Choosing the right technology—be it 3D printing, CNC machining, or injection molding—depends on the product's design and intended purpose.
3. Prototype Fabrication
This is where the actual creation of the prototype takes place. Skilled technicians utilize advanced manufacturing tools to turn design ideas into reality.
4. Testing and Evaluation
Once the prototype is fabricated, it undergoes a series of tests. Feedback from these tests is crucial for making necessary adjustments before moving to full production.
Best Practices for Successful Prototype Manufacturing
To ensure the best outcomes in your prototype manufacturing project, consider implementing the following best practices:
- Maintain Clear Communication: Regular updates and meetings with the manufacturer can prevent misunderstandings.
- Emphasize Quality: Prioritize quality control at every stage of the prototyping process.
- Stay Flexible: Be prepared to adapt designs based on feedback and testing results.
- Involve Stakeholders Early: Bringing stakeholders into the process from the start encourages collaborative input and investment.
Case Studies: Success Stories in Prototype Manufacturing
Let’s examine a few case studies where effective prototype manufacturing led to successful product launches:
1. Tech Gadgets Inc.
Tech Gadgets Inc. utilized a prototype manufacturer to develop a groundbreaking smartwatch. Through iterative prototyping, they refined the user interface and resolved hardware issues, resulting in a highly acclaimed product launch.
2. Eco-Friendly Packaging Solutions
By creating a functional prototype of a biodegradable packaging product, this company gained key insights into user interaction and market fit, which was pivotal for their subsequent funding round.
The Future of Prototype Manufacturing
As technology evolves, so too does the field of prototype manufacturing. The integration of technologies such as AI and IoT promises to revolutionize how prototypes are designed, tested, and produced.
1. Additive Manufacturing
3D printing continues to gain traction as a leading method for prototype creation, allowing for rapid, cost-effective manufacturing of complex geometries.
2. Virtual Prototyping
Using simulation software, businesses can create virtual models to evaluate performance and design effectively without the immediate need for physical prototypes.
Conclusion
In conclusion, the role of a prototype manufacturer is integral to the product development lifecycle, helping businesses mitigate risks and create products that meet consumer demands. By understanding the processes, benefits, and best practices involved in prototyping, companies can make informed decisions that pave the way for innovative and successful products. Engaging with specialized manufacturers like Deep Mould ensures a collaborative approach toward turning visions into reality, ultimately driving growth and success in the marketplace.