Transforming Ideas into Reality: The Power of Rapid Prototyping Plastic Injection Molding
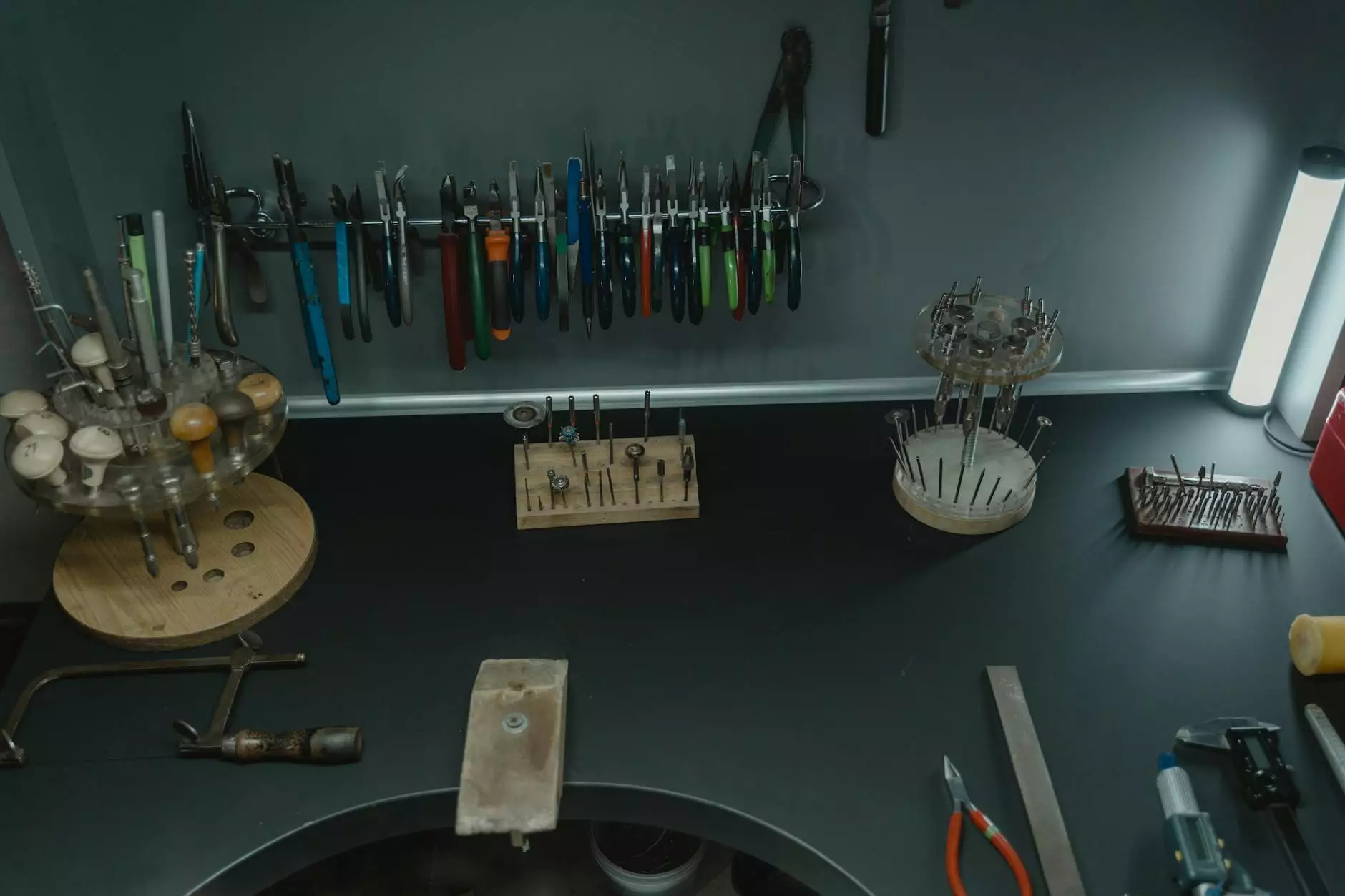
In today's fast-paced industrial landscape, rapid prototyping plastic injection molding has emerged as a powerful tool that is transforming the way businesses design, manufacture, and bring products to market. This innovative process not only accelerates production timelines but also enhances the quality and precision of components. As we delve deeper into the intricacies of this technology, we'll explore its applications, benefits, and how it is reshaping industries across the globe.
What is Rapid Prototyping Plastic Injection Molding?
At its core, rapid prototyping plastic injection molding is a manufacturing technique that allows for the quick production of prototype parts and tooling through injection molding technology. It combines rapid prototyping techniques with the established process of injection molding, enabling the speedy creation of accurate and functional plastic parts.
This process typically involves the following stages:
- CAD Design: The first step is to create a digital model of the component using Computer-Aided Design (CAD) software.
- 3D Printing or CNC Machining: The next step involves creating a mold, often done through 3D printing or CNC machining, which significantly reduces the time required to create molds traditionally.
- Injection Molding: Once the mold is ready, molten plastic is injected into it to form the prototype part.
- Post-Processing: After the part is cooled, it may undergo finishing processes such as trimming, polishing, or assembly before it is ready for testing.
The Importance of Rapid Prototyping in Business
Rapid prototyping is indispensable for businesses, especially in the product development phase. Here are several reasons why:
- Speed to Market: Companies can move from concept to prototype in a fraction of the time traditionally required, allowing them to respond to market demands and changes quickly.
- Cost-Effectiveness: By identifying design flaws early in the process, businesses can save considerable amounts on production costs, minimizing waste and reducing overheads.
- Enhanced Collaboration: Prototypes provide tangible models that stakeholders can analyze, thereby facilitating discussions and collaborations to refine the product.
Applications of Rapid Prototyping Plastic Injection Molding
The applications of rapid prototyping plastic injection molding are extensive and varied, spanning across multiple industries:
Aerospace and Automotive
The aerospace and automotive industries rely heavily on rapid prototyping to create complex parts that are lightweight and structurally sound. Through rapid prototyping, manufacturers can produce intricate designs that meet stringent safety standards while also allowing for design iteration and testing.
In the realm of consumer electronics, rapid prototyping enables the development of functional prototypes quickly. Whether it's housings for smartphones or components for wearable technology, this process speeds up the innovation cycle and ensures that products meet user needs effectively.
Medical Devices
The medical field benefits significantly from rapid prototyping. It allows for the creation of custom implants, surgical tools, and diagnostic devices tailored to individual patient needs, which can be developed and refined rapidly before going into full-scale production.
Benefits of Using Rapid Prototyping Plastic Injection Molding
The advantages of utilizing rapid prototyping plastic injection molding are numerous, and they extend beyond merely speeding up the development process:
1. Precision and Quality
One of the most significant benefits is the high level of precision offered by this method. With advanced technology, manufacturers can achieve tight tolerances and ensure that each prototype meets exact specifications, which is crucial for functional testing.
2. Material Versatility
This process supports a wide range of thermoplastic materials, including engineering-grade plastics suitable for functional prototypes. This versatility allows designers to accurately assess how the material will perform in a real-world environment.
3. Improved Design Innovation
Rapid prototyping encourages creativity and innovation. The ability to quickly produce a prototype enables designers to experiment with different design options and optimize their products without the fear of incurring high costs.
Challenges to Consider
While the benefits are substantial, it is also essential to understand the challenges associated with rapid prototyping plastic injection molding:
- Initial Setup Costs: Although the cost per unit can be low, the initial investment for molds and equipment can be significant, particularly for small businesses.
- Learning Curve: Companies may face a learning curve when integrating rapid prototyping into their workflow. Training staff and adapting to new technologies can require resources and time.
- Material Limitations: Not all materials are suitable for rapid prototyping. While many high-quality plastics are available, certain high-performance materials may not be accessible through this method.
Future Trends in Rapid Prototyping
As technology progresses, several trends are likely to influence the future of rapid prototyping plastic injection molding:
Increased Automation
Automation in the design and manufacturing processes will lead to greater efficiency, reducing errors and speeding up production times significantly.
Advanced Materials
Research continues into newer materials that could enhance the capabilities of rapid prototyping. The development of composite materials, for instance, holds the potential to widen the scope of applications.
Integration with IoT and AI
The integration of the Internet of Things (IoT) and Artificial Intelligence (AI) into the rapid prototyping process can lead to smarter manufacturing solutions. These technologies will enable real-time monitoring, predictive maintenance, and smarter design iterations.
Conclusion
In a world where speed, precision, and innovation are paramount, rapid prototyping plastic injection molding stands out as an invaluable tool for manufacturers. By shortening development cycles and enhancing product quality, it grants businesses a competitive edge in today’s marketplace. Understanding its applications, extending benefits, and being cognizant of challenges equips industry players to harness this technology effectively.
As businesses continue to seek ways to streamline production processes and meet consumer needs with greater efficiency, the future of rapid prototyping in plastic injection molding looks exceptionally bright. Embrace this innovative manufacturing technique and watch your ideas transform into reality.